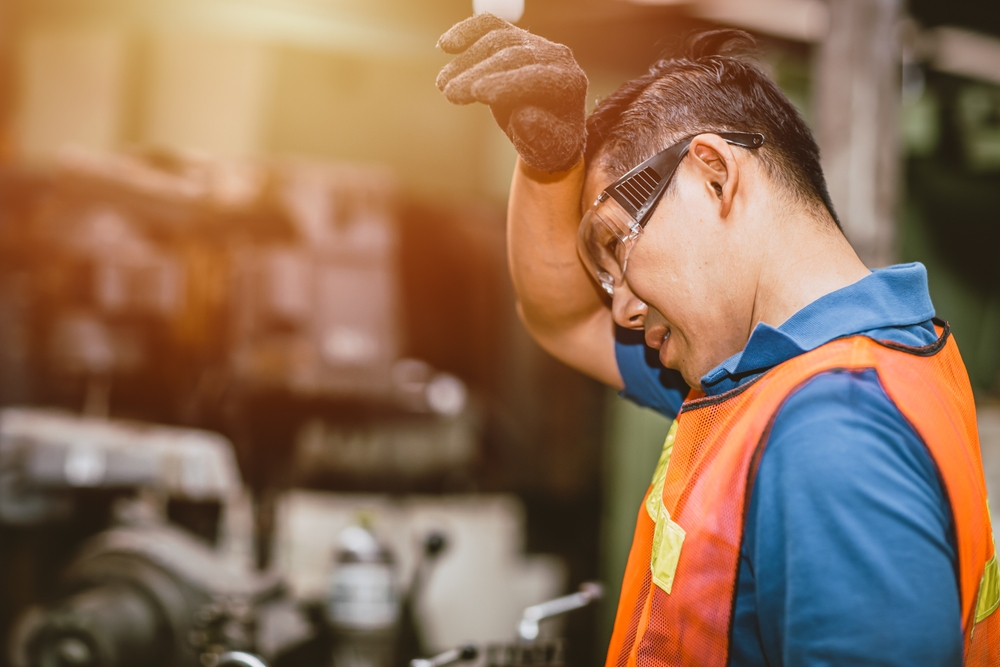
How Weather and Climate Impact Industrial Rubber Lining Longevity
From UV radiation and extreme heat to humidity and freeze/thaw cycles, the environment surrounding your facility can accelerate wear, reduce elasticity, or even cause early failure in rubber-lined systems. Here’s what you need to know, and how you can counteract mother nature’s toll on your equipment.
The Role of Rubber Lining in Harsh Environments
Rubber linings are commonly used in industries like mining, chemical processing, water treatment, and power generation. These linings are engineered to withstand these industries’ harsh exposure, but their performance can be compromised when subjected to intense weather-related stress, particularly in outdoor applications.
Environmental stress can cause:
- Hardening or embrittlement of the rubber
- Surface cracking or crazing
- Loss of flexibility and elasticity
- Delamination or debonding from the substrate
- Accelerated wear and tear
Over time, these effects can reduce containment integrity, increase the risk of leaks, and shorten the overall lifespan of the lining.
Top 4 Weather Conditions That Impact Rubber Lining
These environmental conditions can lead to premature failure of industrial rubber linings if no special prohibitive measures are in place.
1. Extreme Temperatures
Rubber materials are sensitive to temperature fluctuations. High heat can accelerate oxidative degradation, causing the rubber to harden and lose flexibility. In colder climates, rubber becomes more brittle and prone to cracking.
- At high temperatures (above 140°F/60°C), most rubber compounds begin to lose mechanical strength.
- In freezing conditions, rubber can shrink and crack, especially if moisture is present in or beneath the lining.
Selecting rubber compounds rated for the expected temperature range is essential for maintaining performance. For example, EPDM (ethylene propylene diene monomer) rubber performs well in both hot and cold conditions, while natural rubber is less tolerant of heat and UV.
2. UV Exposure
Ultraviolet radiation from the sun can break down molecular bonds in rubber, a process known as UV degradation. Over time, this leads to fading, discoloration, surface chalking, powdering, microcracking, and/or hardening.
Rubbers like chlorobutyl and EPDM offer superior resistance to UV degradation. In high-exposure environments, adding a UV-resistant topcoat or paint layer can significantly extend the life of the lining.
3. Humidity and Moisture
High humidity accelerates the aging process of rubber and promotes the growth of mold, algae, or microbial contamination under the lining. Moisture ingress can also weaken the adhesive bond between the rubber and substrate.
In tropical or coastal climates, where humidity is consistently high, it’s important to:
- Use closed-cell rubber linings to limit water absorption
- Seal all edges and seams properly during installation
- Conduct routine inspections to detect bubbling or debonding
4. Freeze/Thaw Cycles
Regions that experience frequent freeze/thaw cycles pose a unique challenge. Water that penetrates under the lining or into surface imperfections can expand as it freezes, exerting pressure that leads to cracking or spalling of the rubber.
This cycle of freezing and thawing repeatedly stresses the lining system, often causing failure over time unless proactive measures are taken.
How to Avoid Weather Damage to Industrial Rubber Lining
You can’t control the weather, but you can take several steps to prolong the lifespan of rubber-lined assets amidst harsh conditions.
Choose the Right Rubber Compound
Select a rubber formulation designed to withstand the local climate. For example, EPDM or butyl rubber are typically ideal for outdoor use due to their UV, ozone, and temperature resistance.
Use Protective Coatings or Topcoats
Adding an external protective coating (like polyurethane or UV-resistant paint) can shield the rubber from sunlight and weather. These coatings also help resist mechanical abrasion and chemical attack.
Implement Regular Inspection and Maintenance
Routine visual inspections and spark testing can identify early signs of wear, cracking, or debonding. Inspections should be more frequent in climates with extreme temperatures or high moisture.
Avoid Water Traps and Promote Drainage
Ensure that the design of the tank or equipment promotes proper drainage. Pooled water or trapped moisture increases the risk of freeze/thaw damage and microbial growth.
Control Storage and Application Conditions
During rubber lining installation, temperature and humidity levels must be controlled to ensure proper bonding and curing. In-field repairs should be scheduled during favorable weather windows to avoid curing failures.
We’ll Help you Plan for Longevity, Regardless of Climate
Rubber linings are a reliable, long-term protective solution for industrial equipment, but only when matched to their environment. By understanding the threats and implementing smart strategies like proper material selection, protective coatings, and proactive maintenance, we can help you extend the life of your rubber-lined equipment.